Innovative Technologies (robotics, Automation, It), Optical Technologies (research And Technology), Basic Software And System-oriented Software, Cloud & Industrial It Services, Digital Factory Services, Industry-specific Automation Software Solutions, Software And Solutions For Specific Sectors, The industrial level sensors are devices that can be used to monitor or determine the liquid or solid level in a vessel, tank, or any other container used as part of a system or process. The voltage ratio between the tank wall and the probe will be taken to determine the level. However, the tuning fork sensors can be used in conjunction with continuous level detection systems, acting as alarm points for leaks and over-filling. Anything that deflects or absorbs the signal, or acts as a false surface, may cause erroneous readings. The ultrasonic transducer, in transmit mode, generates a high-pressure sound wave (similar to a loudspeaker) that propagates to a target and then reflects back from the product surface (echo). On the other hand, the continuous optical level sensors, use the highly intense laser light that can instill dusty environments, and notice liquid substances. They are preferred for their ruggedness in outdoor environments where reliability is paramount. They are also available in contact and non-contact configurations meaning some of which can be attached outside the container/tank. The trick is really to use an ultrasonic sensor with double the needed range. Our ultrasonic level sensors are commonly paired with an appropriate controller for flow calculations over open channels. How thick/viscous is the material?
The minimum detection distance is really controlled by lengthening your blanking distance, which is a short distance right in front of the sensor face where nothing can be detected (see individual sensor specifications). If it does, you lucked out. Install Guides This device also consists of a piezoelectric element to pick up the frequency of the vibrating fork.
These sound waves then reflect off the liquid surface you are trying to measure. Rugged, low-power, and rated Intrinsically Safe for hazardous location, with optional Gas Discharge Tube Surge Protection. *G2 polypropylene threads fits 2" NPT. Another great fit for our ultrasonic sensors is open channel flow. When a liquid covers the probe, its electrodes form a part on an electric circuit, causing current to flow which signals a low or high level. These sensors are among the handful of technologies that work well in foam and sticky substances. Are there obstructions/limitations that would block probe or sensor placement? Privacy & Cookie Policy Some of our competitors want you to believe that their lower cost ultrasonic level sensors are just as good as our higher quality line. The variation in the fluid level could be sensed by the level sensor and it would transmit this info to the operator. This type of measurement is done by using a thermistor, the thermistor is a device that would decrease its resistance when there is a rise in temperature. Pros No moving parts, easy to use, low-cost, Cons Invasive, liquids need to be conductive, probe erosion, Applications Tank level measurement for boiler water, reagent monitoring, highly corrosive liquids. The industrial level sensors keep track of the amount of product in storage containers. Although simple in design, this technology offers long-term reliability at an attractive price point. Avoid using ultrasonic level sensors on light powders or especially dusty environments.

UK T: +44(0)1236 459020 F: +44(0)1236 459026, SST Sensing Ltd Company Registration Number SC232226, LOX-EVB LuminOx Evaluation Interface Board, View our Full Range of Level Sensing Solutions, 5 Hagmill Crescent, Shawhead Industrial Estate, Coatbridge, ML5 4NS.
Averaging your readings is a way to smooth out your level changes.

What are the different types of level measurement? Because the speed of sound is constant, under fixed atmospheric conditions, the time from the sound burst to the return is measured and translated into a distance. But most of our ultrasonic level sensors are either used for liquid level, open channel flow, or for presence detection and object profiling, where they perform very well. The LPU-2127 features a built in keypad and LCD display for easy programming that can be done entirely through the keypad. In addition, they do not come in contact with the target substance, which avoids build-up and damage. The float switches utilize a float, a device that will raise or lower when a product is applied or removed, which will open or close a circuit as the level raises or lowers moving the float. Advantages of sight glass level measurement. Pros very accurate, no calibration required, multiple output options, Cons expensive, can be affected by the environment, limited detection range, Applications Moist, vaporous and dusty environments. However, cleaning is required if the lens gets dirty or coated. View the full range of exceptional Level Sensing Solutions from SST Sensing, Cons Invasive, number of uses are limited. The ultrasonic level sensors microprocessor calculates the distance and converts it to a level indication, volume measurement, or a rate of flow. Applications level control of liquid, powders and fine grained solids within mining, chemical processing and food and beverage industries. Ultrasonic sensors require an unobstructed air column between the sensor and the target. If you leave it on high all the time, it will wear down faster, just like a speaker can be blown out by too much volume. The time taken by the wave to reflect back from the fluid is calculated to determine the level.
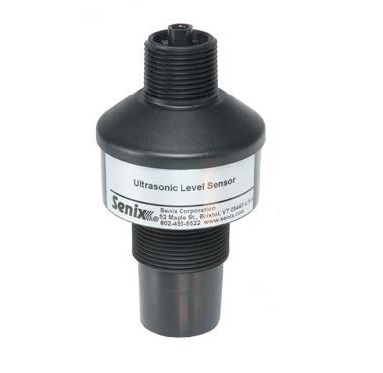
This gives you a much stronger signal that will provide a better echo for your sensor to measure.

Ultrasonic sensors measure levels by calculating the duration and strength of high frequency sound waves that are reflected off the surface of the liquid and back to the sensor the time taken is relative to the distance between the sensor and the liquid. The long probe transmits a low voltage, the second shorter probe is cut so the tip is at the switching point. Although the design is simple, this technology provides long-term reliability at an attractive price point. The capacitance level sensors are commonly used in applications such as tank level monitoring in chemical, food, water treatment, battery industries, and brewery industries. In this type of level sensor, the sensor would be placed parallel to the tank and this device consist of a column with visual indicators and it would show the level. The relay would be switched according to a high, or low level. The float switches only indicate a low/high level, they cannot measure a variable level. Lower averaging and a looser window is required to keep your readings caught up with rapid changes. 1025 W 1700 N Logan, UT 84321Phone: (877) 373-5940Fax: (435) 753-7490 Applications Tank level monitoring in chemical, food, water treatment, power and brewery industries. The target is often uneven and soft. If a standard ultrasonic sensor will not work for the application, Madison can custom engineer a solution in as little as 4 days, once the requirements are established. Let's discuss continuous level measurement sensors first. Call: 203-488-4477, 27 Business Park Drive Based on what mounting style the user selects heavily depends on the construction and design of the tank or container the switch will be positioned. This means that youll never know if their ultrasonic sensor will work for you. It can also compensate for temperature, and filter the signal. Accurate measurement of liquid volumes at any point in a container is critical for many commercial and industrial processes. Branford, CT, 06405, Phone: 203-488-4477 Open channels are a primary means of transporting, filtering, and metering water. The reflected wave is then converted to an electrical signal that is converted to give the distance to a specific target. Ultrasonic sensors are well suited for some of them. For this purpose, we will use the term Optical Level Switch.
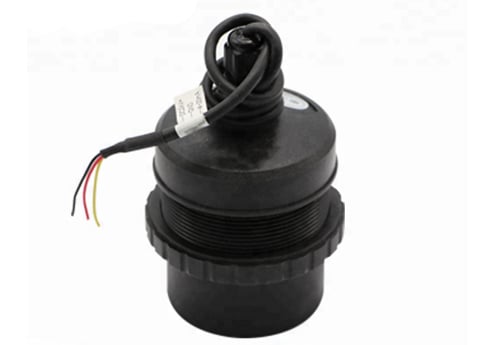
In this type of level measurement, a glass gauge is used and it will be placed close to the pressurized tank. The industrial level sensors include a wide range of technology from simple levers to gamma-ray detection and are used in almost any application with a liquid in a tank or solid product in a granular form. Aerospace Vendor Terms Balancing pulse strength and sensitivity is crucial to a reliable measurement and a durable sensor. As this type of technology is contact based, the reliability of these sensors can be heavily influenced by fluids sticking to the probe. This method is quite accurate, and weve developed a line of sensors with an accuracy of 0.25% of detected range. These types of sensors are very easy to use and clean as they don't have any moving components. The frequency of the fork changes when the fork is submerged in the media and this change is detected by the internal oscillator and converted into a digital output signal. Terms & Conditions Classification of a level sensor according to the sensing point. Let's discuss point level indication sensors first, beginning with capacitance level sensors.
Different kinds of industrial level sensors are employed in manufacturing and industrial process control settings and systems. Trip points help you control pumps, alarms, and valves easily.
They are also suitable for detecting leaks preventing costly damage. Within minutes, you can perfectly match your sensors parameters to your application, giving you unparalleled performance.

Capacitance level sensors operate in the way that process fluids have dielectric constants, significantly different to air. Advantages of thermal dispersion level sensor, Applications of thermal dispersion level sensor. This type of level measurement is done by measuring the voltage ratio change between the measurement rod and tank wall which contains the process fluid. Advantages of the potentiometric level sensor, Disadvantages of the potentiometric level sensor, Applications of the potentiometric level sensor. Also called resistive level sensors or conductive probe sensors. Used in systems that require remote monitoring. Vendor Compliance Manual, Automation Products Group, Inc. In this type of level measurement, the measurement of the liquid level is done by measuring certain parameters such as pressure, temperature, weight, etc. Are you measuring a liquid or solid (bulk)? So when the fluid level in the tank changes then the dielectric constant would change and thus the capacitance would vary. The float would sink to the bottom of the fluid and then it would float on the top of the fluid which is to be measured. Fax: 203-481-5036 It can be used with different fluid densities, The measurement is possible if there is a large amount of liquid, It can be used to measure the level of water, oil, hydraulic fluids, and chemicals, It can be used for high temperature and pressure, Fluid density change would affect the measurement, Only non-corrosive liquids can be measured, It cant be used with dangerous process fluids, It can be operated in high temperature and pressure, It cant be used with varying dielectric materials, It cant be used with media that coats the sensing element, Measurement is affected by the variations in temperature, It can only be used with conductive liquids, It can be used with highly corrosive liquids, It can be used for solid and liquid level control, It can be used with media that exhibit sticky properties or foam, It is independent of the media characteristics, It cant be used for continuous level measurement, It is used to control the maximum amount of solids and liquids in many applications such as grains, cement, granules, powder, It can be used to do the level control of paste or adhesive media, It can be used to do the level measurement of small tanks, A specified amount of conductivity is required for the media, It can be used with sticky or foaming media, Measurement is not affected by the type of media which is to be measured, High pressure and temperature could affect the measurement, Reflections could happen due to agitation, Foam, steam, change in concentration would affect the measurement. This can result from physical obstructions, excessive foam, heavy vapors, thick dust and light powders. There are a range of technical terms used to describe this type of level sensing technology. For large tanks and industrial applications However, very accurate level information can be obtained with radar and also compensate for fixed structures within the container. The ultrasonic sensor calculates the distance to the target based on the amount of the time that it took for the sound wave to return to the transmitter. Due to this the force that acts on the spring would vary and thus the spring would compress. Level sensors are classified according to the number of locations where the fluid measurement is to be done. The float switches are non-powered devices that provide a direct indication. So the intensity of the received signal is used to determine the level of the process fluid. Advantages of the radiometric level sensor, Disadvantages of the radiometric level sensor, Applications of the radiometric level sensor. Careers, ISO 9001:2015 Certification In this type of level measurement, the fluid conductivity is utilized to do the measurement. Pressure, moisture, turbulence, and temperature influence the ultrasonic sensor's response. Simply tell the sensor how many samples (singular readings) you want to average. They are also used in systems in which temperatures vary. The float level sensor is composed of a magnet and also a magnetic reed switch, the float would vary its position according to the change in the liquid. The float switch sensors are commonly used in tank level applications where oil, water, chemicals, and hydraulic fluids are being used. The tuning fork vibrates at its mechanical resonance frequency of approximately 1200 Hz and is piezo-electrically energized. The vibrating sensors are perfect for solid and liquid level control, including foam and sticky materials, as well as fine-grained solids and powders. Other uses include presence or absence detection, and object dimensioning.

This type of level sensor is used where the level measurement at all locations must be done. These level changes are converted into analog signals. The radar sensors are unaffected by dust, temperature, or pressure. The float moves with the change in liquid and will cause the reed switch to either open or close depending on if its in air or liquid. post-graduate in Electronics & communication.
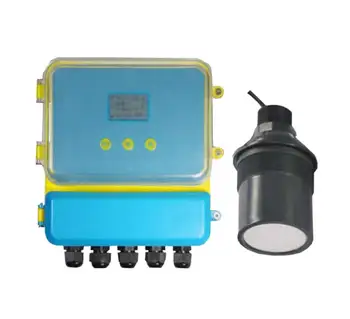
The optical sensors work based on the changes of transmission in infrared light emitted from an IR LED. Generally, the probes are made of conducting wire by PTFE insulation.

We shall start with industrial ultrasonic level sensors. The liquid level is the position of a liquid surface above or below a reference point. Controlling the response speed to changing levels is very helpful for filtering out a lot of noise. Measurement is not affected by the media properties such as foam, vapor, density, etc. Advantages of the conductive level sensor, Disadvantages of the conductive level sensor, Applications of the conductive level sensor. However, they may require calibration and can only be used in certain liquids. While you're here, check out our high-quality and insightful articles.
So the time taken by the waves to reflect back from the media is calculated and thus the level can be determined. If you have a fast moving target, then youll want to be careful here. sales@apgsensors.com. This is a moving window that follows the current accepted reading. Blog Filtering out unwanted echoes with your ultrasonic level sensor is easy with a few different settings. This type of level sensor would detect the surface or interface of the liquids and the variation in the density of the measured substance wont affect the measurement.
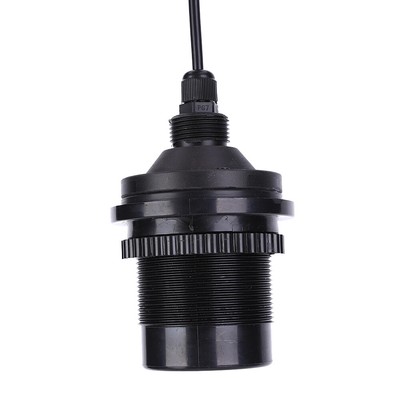
Besides, they are non-invasive, as they don't have to touch the product that's sensing. The disadvantages of these sensors are they are invasive, can only sense conductive liquids, and the probe will erode over time. News Two conductive probes are used in this one of them is a short probe so when the fluid is not in contact with the probe then the electrical resistance between the probe and the and vessel would be really high. If you have to turn up your sensitivity too much, youll start to pick up unwanted echoes and erroneous readings. Along with the window, youll set the number of samples the sensor needs to detect out of the window before it validates as a new level. So if you have your pulse strength ramped up as high as you can just to get a good return signal, it means your sensors isnt powerful enough. And while technologies new and old promise optimum performance, ultrasonics will remain a staple for continuous non-contact measurement. Programming our ultrasonic level sensors is relatively easy, and is usually done well in under 30 minutes. What are the application's operating temperature and pressure ranges? The liquid which is to be measured could be in a tank or it would be in natural forms like a lake or river. Most of our ultrasonic sensors are designed for use in level applications with ranges from as little as 4 inches to as much as 50 feet. This type of level measurement is done by transmitting gamma source and in order to do that cesium or cobalt isotope is used as the source. From time to time, we get some customers who try some very interesting things with ultrasonic sensors - even if we express some skepticism. Theyve been used on everything from race cars to apple harvesters, some more successfully than others. You may still opt to use an ultrasonic in a dusty environment if youre willing to wait for a good level reading once the dust settles. Happy Reading! Another very popular application for ultrasonic sensors is solid level detection. This is similar to the float switch and it has a magnetic sleeve and this would be attached to the spring so when the spring moves the magnet would move along it and thus switching would be done. This series features, This short range ultrasonic level sensor is designed with flexibility in mind, this.
There are many technologies designed for detecting objects and controlling the movements of machines and robotics. Other manufacturers dont include trip points in their ultrasonic level sensors, forcing you to spend another couple hundred dollars on a module. There are three main settings you can adjust: The pulse strength control lets you fine tune sound wave bursts for optimal detection for your application. However, our continuous float level transmitters and submersible pressure transducers may be best in these scenarios. When a product is present at a certain point, it is specified by point level measurement, whereas continuous level measuring indicates the continuous level of a product as it rises and falls. All rights reserved. The industrial ultrasonic level sensors have no moving parts, are compact and cost-effective, reliable, and non-invasive. Thank you for your interest in publishing an article with Packaging-Labelling. The sensitivity setting gives you control over how hard the sensor will listen for echoes. In this type of level measurement, a buoyant object will be placed between the fluid which is to be measured and also the headspace vapor in the tank. Our Engineers have over 60 years combined experience in the sensor industry. The transducer then switches to receiver mode (similar to a microphone) to listen for the reflected wave (echo). The medium which is to be measured could be stored in a vessel, bins, silos, etc. A more powerful sensor can also be used to strengthen the signal. Their usage extends past manufacturing and industrial environments, and they are the driving device in the fuel level gauges in most airplanes, cars, and boats. Applications of Capacitive sensor Proximity, Gaging Displacement, Level measurement. They can be used as low-level indicators to avoid run dry conditions when using coolant, oil, or hydraulics. The rise in the production of vehicles, the development of smaller, smarter, and cheaper sensors, and supportive government regulations are the major factors that are expected to be driving the industrial level sensors market. You want your pulse strength only as high as is necessary to get a good return signal. Pros Solid-state, can be non-invasive, compact, accurate, Cons May require calibration, can only be used in certain liquids. All Right Reserved. However, radar can provide very precise level information and also compensate for fixed structures within the container. Two versions are available, one for fluids with high dielectric constants and one with low dielectric constants. This parameter would be calculated to determine the fluid level. Besides, they are small, inexpensive than other sensors, accurate, and invasive to the product. Setting a maximum and minimum detection distance simply causes the sensor to ignore any echoes outside of that range. Capacitance level sensors work with a range of solids, liquids, and mixed materials. Our ultrasonic level sensors are known for their field programmability.
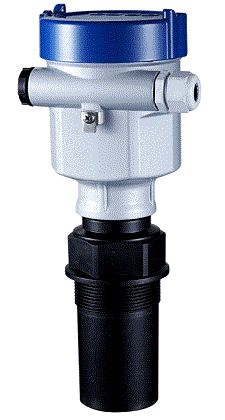
Reflected light, such as in a small reflective tank, mirrored tanks, bubbles, milk or coating fluids can often cause issues with delayed readings. Ultrasonic sensors work by sending sound waves that echo off of a target and return to the transmitter. Cons Invasive as the sensor requires contact with the liquid, requires power, certain thick substances can cause coating on the prism. This magnetic float would also move the visual indicators in the column. Ultrasonic level sensors are typically quite small, low maintenance, and easy to ship and install. These sensors are also capable to detect the powder levels and also the interface between the liquids. Essentially, youre causing your sensor to double check the changes in the level before it serves it to you as an output. What is the dielectric constant for the media? Unlike a speaker, the ultrasonic transducer - the part that makes and receives the sound waves - wont blow out, but will wear down over time. Being a solid-state device, these compact switches are ideal for a vast range of point level sensing applications, especially when reliability is essential. Common uses for ultrasonic level sensors are level, volume, and flow monitoring.
Ultrasonic technology should be considered in vented or non-pressurized applications: Ultrasonic sensors are used to continuously measure semi-solid, corrosive, and viscous medias, slurries and even some solids. When the sensor tip is in air, the infrared light inside the sensor tip is reflected back to the detector. If the container is linear, then inferring a volume measurement is easy. User Manuals We not only offer them built into the sensor, but we offer them at no additional cost. In this type of level sensor, a displacer is used and spring would be connected to the displacer.
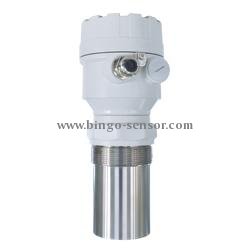
To ensure your ultrasonic level sensor is able to properly measure the surface, a stilling pipe can be used to contain or guide the signal around obstructions, or to lessen surface foam. Will the substance coat or put up up on surfaces? The tuning fork sensors are cost-effective and compact, easy to install, invasive to the product, and essentially maintenance-free. One such technology is ultrasonic. The operation of radar or microwave sensors is similar to ultrasonic. sensing range to 32 ft Some equipment manufacturers may also be surprised at both the variety and intelligence of level sensing alternatives available on the market. U3M-148 compact ultrasonic sensor, 1" NPT Sensing range to 6 ft deep, NEW! The reed switch would open or close and it is dependent if it is in the air or in liquid. They work by emitting and receiving ultrasonic waves, at the range of frequency from 20 to 200 kHz. But it doesnt stop there! Before selecting a level meter, controller, or any other level measurement instrument, make sure you have the answers to the following main questions. They measure the change in capacitance between two plates produced by changes in level.
Advantages of the hydrostatic level sensor, Disadvantages of the hydrostatic level sensor, Applications of the hydrostatic level sensor. Is the application a novel installation or retrofit or existing process installation? The IRU-9400 is an indoor sensor with a more sensitive transducer to detect difficult targets such as reflective and soft. COPYRIGHT 2020 Automation Products Group, Inc. How Does An Ultrasonic Level Sensor Work. The waves are then replicated back to a transducer. Toll-Free: 800-466-5383 Advantages of the ultrasonic level sensor, Disadvantages of the ultrasonic level sensor, Applications of the ultrasonic level sensor. What are different kinds of level switches? Each of our ultrasonic sensors have a microprocessor, which allows for more advanced control. The good news is, youll likely be able to use AutoSense, which automatically adjusts pulse strength and sensitivity to optimum settings. Several of our models are a good fit for this application. The probe will be placed inside the tank, the metal wall of the tank, and the probe would act as two capacitor plates. In non-linear containers, a strapping chart is often used to adjust the reading to a volume as level rises and falls. What kind of output do you needanalog, relay, digital display, etc from the sensor?

In addition, the sensor needs to be calibrated to the specific material to excuse the varying dielectric constants and differences in the tank design. They can be used indoor or outdoors, are low maintenance and can be cost-effective in difficult applications. Typically, suppliers will offer a range of mounting options, with the most common being horizontal/side mounting and vertical mounting. What are the chemical properties of the product to stability and corrosiveness? This sensor would determine the tank pressure and this pressure will be proportional to the liquid level. Refer to the specifications to make sure you find a sensor that will work well for you. Ultrasonic sensors work on the basic principle of sound waves (mechanical energy) to determine material level. Ultrasonic level sensors are good in many of these applications because of their ability to handle adverse conditions. The disadvantages of a float switch are they are invasive to the product, have moving parts, and can be large in size. Conductivity level sensors also have no moving parts, are low cost, and fairly easy to use.
Madisons trained experts will consider fluid composition, chemical compatibility, container size and shape, agitation and by-products (foam or vapor), and level range to provide the correct solution. They are also utilized in systems in which temperatures differ. Having the programming options on one of our ultrasonic level sensors ensures you can get the performance you expect. Liquid level sensors have been around for decades, in markets such as food and beverage, industrial, medical and domestic, printing, agriculture, automotive and white goods for leak detection or level measurement.We often wonder why customers choose one technology over the other and it is a common question we are asked. Our client success team member will get in touch with you shortly to take this ahead. But is there need for such technologyor any level sensing device is the question that many people may ask. An immense use for float switches is in liquid storage tanks for high or low-level indication. Capacitance, Optical, Conductivity, Vibrating (tuning fork), Float Switch are the sensors for point level indication, while Ultrasonic and Radar (Microwave) are the sensors for continuous level measuring.
Sitemap 39