It is also perfect for applications where precision parts are required, since the 33 percent smaller diameter stream enables more intricate inside corner cutting down to a 0.015 in radius.
Early waterjet cutting systems adapted traditional systems such as mechanical pantographs and CNC systems based on John Parsons 1952 NC milling machine and running G-code. [23] Hashish, who also coined the new term abrasive waterjet, and his team continued to develop and improve the AWJ technology and its hardware for many applications which is now in over 50 industries worldwide. The magazine delivers the news, technical articles, and case histories that enable fabricators to do their jobs more efficiently. VELOCITY MATTERS Nozzle size is not the only factor that determines the ideal mesh size for a given application. Is used for machining a large array of materials, including heat-sensitive, delicate or very hard materials. A good starting point is 20-50 HP and 60 KSI of pressure and a jewel size of 0.011 in. The largest waterjet manufacturer, Flow International (a spinoff of Flow Industries), recognized the benefits of that system and licensed the OMAX software, with the result that the vast majority of waterjet cutting machines worldwide are simple to use, fast, and accurate. Chadwick, Ray F Chadwick, Michael C Kurko, and Joseph A Corriveau. [45], Due to its relatively narrow kerf, water jet cutting can reduce the amount of scrap material produced, by allowing uncut parts to be nested more closely together than traditional cutting methods. HYPERPRESSURE VS. NORMAL PRESSURE As pressure has increased in waterjet cutting over the years, so has jet speed. (first view), Optimizing the tool path for acceleration and deceleration to control the stream while its in the material and utilizing taper compensation to get a high precision cut in a quicker time frame have each contributed to more efficient cutting at any pressure. For example, 4 inches (100mm) thick aluminium Q5 would be 0.72in/min (18mm/min) and Q1 would be 4.2in/min (110mm/min), 5.8times faster.[54]. The system was an overhead gantry design, similar in overall size to the HS-1000. 2022 FMA Communications, Inc. All rights reserved. To frame the discussion, lets remove the intensifier versus direct-drive pumps argument.
Maintenance is easier since the new pump is designed for fast, foolproof maintenance with a special high-speed pressure loading tool provided with the pump. The air used as a carrier medium for transporting the abrasive into the mixing chamber also becomes part of the AWIJ, which now consists of three components (water - abrasive - air). Of course, setting the optimal pressure is just a starting point. As long as these materials form the foundation of all abrasive waterjet cutting, horsepower and pressure will play major roles.
[7] Research by S.J. On the flip side of the argument, it is possible to achieve 60,000 PSI with a 5-HP pump, but the applications are severely limited, and the orifice would be absurdly narrow. Even with the perfect balance between garnet mesh size, pressure, horsepower, and orifice/nozzle diameter, equally perfect cycle times and profitability can remain out of reach. Water jets use approximately 0.5to 1USgal (1.93.8l) per minute (depending on the cutting head's orifice size), and the water can be recycled using a closed-loop system. orifice, a 50-HP intensifier pump running at 60,000 PSI generally will output 1 gallon per minute (GPM). [3] These early applications were at low pressure and restricted to soft materials like paper. [9] In the early 1970s, the desire to improve the durability of the waterjet nozzle led Ray Chadwick, Michael Kurko, and Joseph Corriveau of the Bendix Corporation to come up with the idea of using corundum crystal to form a waterjet orifice,[10] while Norman Franz expanded on this and created a waterjet nozzle with an orifice as small as 0.002 inches (0.051mm) that operated at pressures up to 70,000psi (480MPa). Therefore, comparatively deeper or faster cuts can be made with the AWSJ. A 220-mesh garnet will provide smoother, more accurate finishes over 80 mesh, especially when cutting thin material. Typical distance is .125in (3.2mm). At 60,000 psi, the garnet abrasive accounts for over half of the cost. jetting pressure water nozzles The abrasive is pulled into the cutting head from very low velocity via a venturi effect (a way of creating suction) and then accelerated down the mixing tube by the supersonic water, as shown here. nozzles, a mesh of 120 or higher is optimal. 3: How to loosen die grinder collets and gas bottle caps, Penn College welding students, metal artist build all-steel motorcycle, 2022 FAB 40: Diversification drives the metal fabrication business model, How stamping press controls have evolved to keep up with automation, Conference focused on how EVs impact stamping makes in-person debut, A game plan to reach out to the next generation of creators, Die Science - Stamping Die Essentials: Determine the process first, Top high school, college welders announced in national SkillsUSA competition, Consumables Corner: Why a shop using GMAW with C25 shielding gas experienced porosity, Jim's Cover Pass: Dealing with leadership change in the weld shop, Playing With Fire: A challenge to metal fabrication's skills gap conversation, Combining a love for motorsport racing and metal fabrication, Tube 2022: Innovation, will to beat market forces are common themes in Dsseldorf, The power (and necessity) of flexible schedules in manufacturing, Diagnosing electrical/hydraulic problems in a CNC tube bender, La realidad sobre la porosidad de la soldadura, Los robots para fabricacin de metal se vuelven mviles, Mantenga las piezas de trabajo en movimiento, Six trends to consider about the future of additive manufacturing, A better way to assess the tensile strength of 3D-printed parts, What 'newbies' don't know and should know before plunging into 3D printing, SafanDarley R-Brake 130T the flexible bending cell.
Proper waterjet cutting pressure comes from a combination of pump horsepower and nozzle and orifice diameter. [1], Waterjet cutting is often used during the fabrication of machine parts. For smaller nozzles used for high-precision applications, such as 0.014- or 0.010-in. In fact, the smaller diameter of the jet that comes from a high-pressure system may be more effective in water-only cutting applications, such as food products or foam rubber. Every pump has a maximum operating pressure, so to gain the benefits of a higher velocity stream a pump must be designed to operate at higher pressure. Its also not practical for applications where actual cut speed and cost per part is a small portion of the total cost to produce the part. vac truck root cutter tools jet sewer vactor cutting parts cutters hydraulic hydro The abrasive is pulled into the cutting head from very low velocity via a venturi effect (a way of creating suction) and then accelerated down the mixing tube by the supersonic water (Figure 2). For thin materials, the difference in cutting speed for Q1 could be as much as 3 times faster than the speed for Q5.
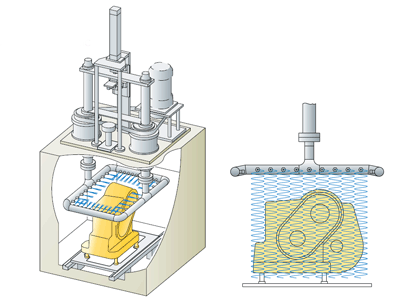
Both vehicles will get you from point A to point B; the question really comes down to how nice the ride is. By the mid-1800s, steam locomotives were common and the first efficient steam-driven fire engine was operational. The horsepower/pressure combinations shown in the chart might be considered optimal on paper, but they in no way account for what may be happening in your machine. The interaction of the water jet in the mixing chamber with the air inside creates negative pressure, the water jet entrains air particles. nozzle orifice at 60 KSI is constrained to a 0.010-in. Walker in the mid-1960s expanded on traditional coal waterjet cutting to determine ideal nozzle shape for high-pressure waterjet cutting of stone,[8] and Norman Franz in the late 1960s focused on waterjet cutting of soft materials by dissolving long chain polymers in the water to improve the cohesiveness of the jet stream. Pressure is determined by the volume of water being pushed through a nozzle orifice by a pump (see Figure 2).
pressure tanks well water wellmate pumps Zimmermann Milling Solutions, a leading global high-tech supplier of portal milling machines, will virtually show three new gantry machines at their booth. What combination of pressure, horsepower, and nozzle assembly is best for a given application? When Ultrahigh-Pressure (UHP) waterjets first came on the market, pressures were in the 36,000 psi range. [6], While not effective for the XB-70 project, the concept was valid and further research continued to evolve waterjet cutting. [26] The abrasive grains become faster with the WASS than with the WAIS for the same hydraulic power of the system. Depending on the cutting head, the maximum cutting angle for the A axis can be anywhere from 55, 60, or in some cases even 90degrees from vertical. As waterjet cutting moved into traditional manufacturing shops, controlling the cutter reliably and accurately was essential. Today, there are two different types of Abrasive Waterjets: The Abrasive Water Suspension Jet (AWSJ) - often called Slurry Jet or Water Abrasive Suspension (WAS) jet - is a specific type of abrasive water jet, which is used for waterjet cutting. head jet water cutting pure waterjet aqualine kmt [43] Sharp corners, bevels, pierce holes, and shapes with minimal inner radii are all possible. Much like sandpaper, finer surface finishes require higher, more fine-grained mesh sizes. Later on the abrasive waterjet entered the scene and began being used for cutting hard materials, including metals, stone, composites, glass, and ceramics. Passing through a small-diameter orifice, the water forms a coherent jet of water that then passes through a venturi nozzle, where a metered amount of granular abrasive is drawn into the water stream. Pressure equals productivity and efficiency because of jet velocity. Commercial water jet cutting systems are available from manufacturers all over the world, in a range of sizes, and with water pumps capable of a range of pressures. A critical development was creating a durable mixing tube that could withstand the power of the high-pressure AWJ, and it was Boride Products (now Kennametal) development of their ROCTEC line of ceramic tungsten carbide composite tubes that significantly increased the operational life of the AWJ nozzle. In contrast to the abrasive water injector jet (AWIJ), the abrasive water suspension jet (AWSJ)[25] is characterised by the fact that the mixing of abrasive and water takes place before the nozzle. Power is proportional to pressure times volume flow rate (P = kp V). Uses a high velocity stream of ultra high pressure water 30,00090,000psi (210620MPa) which is produced by a high pressure pump with possible abrasive particles suspended in the stream. Throughout the history of manufacturing, once the fundamental capability of a process has been established, the next step has always been to make it more efficient striving to make product cheaper and faster. Hashish, Mohamed, Michael Kirby and Yih-Ho Pao, CS1 maint: multiple names: authors list (. However, before the use of HyperPressure pumps became common, many other alternatives to improve productivity were attempted: Other methods that have been employed include optimizing the tool path for acceleration and deceleration to control the stream while its in the material and utilizing taper compensation to get a high precision cut in a quicker time frame. The abrasive then mixes with the water in a mixing tube and is forced out the end at high pressure. The only way to make a waterjet stream go faster is to raise pressure but not through increasing horsepower.
This can be useful for applications like weld preparation where a bevel angle needs to be cut on all sides of a part that will later be welded, or for taper compensation purposes where the kerf angle is transferred to the waste material thus eliminating the taper commonly found on water jet-cut parts. Extremely easy to set up and operate, waterjet cutting technology is a cold-cutting process that can cut virtually any material without adding heat or stress and quickly produce small or large batches of parts, even for difficult projects. Lorincz, Waterjets: Evolving from Macro to Micro. With recent advances in control and motion technology, 5-axis water jet cutting (abrasive and pure) has become a reality. There will also be a clear split in systems that are designed for higher productivity and lower productivity, and pressure will play a significant part in that split. [21] Smiths design was further refined by Leslie Tirrell of the Hydroblast Corporation in 1937, resulting in a nozzle design that created a mix of high-pressure water and abrasive for the purpose of wet blasting.[22]. Leach and G.L. Meatcutting using waterjet technology eliminates the risk of cross contamination since the contact medium is discarded. Others have advocated direct-drive systems that use a mechanical crankshaft pump (see Figure 1). [5] This system used a 100,000psi (690MPa) pump to deliver a hypersonic liquid jet that could cut high strength alloys such as PH15-7-MO stainless steel. sugino machine washing spiral pressure water nozzle jet [15] Higher pressures in hydraulic systems in the oil industry also led to the development of advanced seals and packing to prevent leaks. For materials that are brittle or tend to delaminate, start with a low-pressure pierce and then ramp up for cutting. For a given pump power, any increase in pressure must be matched by a proportional decrease in volume flow rate. orifice. There are many reasons for the rapid acceptance of waterjet technology. Easily access valuable industry resources now with full access to the digital edition of The Tube & Pipe Journal. The correlation between water velocity to pressure. There are two types of pumps used to create this high pressure; an intensifier pump and a direct drive or crankshaft pump. INCREASING WATER VELOCITY BY RAISING PRESSURE If youve ever investigated purchasing a waterjet system, youve probably been hit with an onslaught of marketing and sales data showing the benefits of each. This full 5-axis cutting could be used for cutting contours on various surfaces of formed parts. This beam of water is ejected from the nozzle, cutting through the material by spraying it with the jet of speed on the order of Mach 3, around 2,500ft/s (760m/s). In 1987, Ingersoll-Rand Waterjet Systems offered a 5-axis pure-water waterjet cutting system called the Robotic Waterjet System. Here abrasives such as garnet and aluminium oxide, are fed into the nozzle via an abrasive inlet. A 5-axis cutting head can be used to cut 4-axis parts, where the bottom surface geometries are shifted a certain amount to produce the appropriate angle and the Z-axis remains at one height. Finding the best combination of horsepower and pressure for a given machine is like telling you the best way to drive your car. The difference is that with the HyperPressure pump, the stream and the abrasive added to the stream travels much faster and cuts at twice the speed. For example, a 50-HP intensifier pump with a 0.014-in. Typical water jet cutting machines have a working envelope as small as a few square feet, or up to hundreds of square feet. The technology has evolved and the trade-offs have changed over the years. There are six main process characteristics to water jet cutting: Edge quality for water jet cut parts is defined with the quality numbers Q1 through Q5. For pure waterjet applications performed without abrasives, more pressure may lead to faster cutting. Why is that so? Figure 1 In 1962, Philip Rice of Union Carbide explored using a pulsing waterjet at up to 50,000psi (340MPa) to cut metals, stone, and other materials. Non-abrasive cuts are normally 0.007to 0.013in (0.180.33mm), but can be as small as 0.003 inches (0.076mm), which is approximately that of a human hair. Produces no heat damage to workpiece surface or edges. [48] Examples of materials that cannot be cut with a water jet are tempered glass and diamonds. Waterjet technology evolved in the post-war era as researchers around the world searched for new methods of efficient cutting systems. [17] McCartney Manufacturing Company in Baxter Springs, Kansas, began manufacturing these high-pressure pumps in 1960 for the polyethylene industry. HyperPressure technology is applicable to most waterjet applications today. AWSJ cutting, in contrast to the AWIJ cutting process described below, can also be used for mobile cutting applications and cutting under water, in addition to machining demanding materials. The total cost of ownership over time is less, however, due to reduced material and labor costs. This means the abrasive speed is governed by the water speed. Think of these as a good starting place for optimizing your waterjet cutting on specific material. This negative pressure is used for the pneumatic transport of the abrasive into the chamber (the abrasive is led to a lateral opening (bore) of the mixing chamber by means of a hose). Acrylic and other plastics are excellent candidates for waterjet cutting thanks to the absence of heat transference, but they do tend to have some chipping or cracking issues when piercing. The term abrasive jet refers specifically to the use of a mixture of water and abrasive to cut hard materials such as metal, stone or glass, while the terms pure waterjet and water-only cutting refer to waterjet cutting without the use of added abrasives, often used for softer materials such as wood or rubber. Regardless, the basic principles behind waterjet cutting havent changed. Both play an important role in optimizing waterjet processes, but the relative importance of horsepower and pressure depends entirely on your waterjet application and the condition of the waterjet machine itself. [34] Creating motion control systems to incorporate those variables became a major innovation for leading waterjet manufacturers in the early 1990s, with John Olsen of OMAX Corporation developing systems to precisely position the waterjet nozzle[35] while accurately specifying the speed at every point along the path,[36] and also utilizing common PCs as a controller. chipping water peeling concrete floor pressure type slabs sugino nozzle cyber jet ultrahigh unit frame deep (The jewel is where high-pressure water transitions to high-velocity water.) [11] John Olsen, along with George Hurlburt and Louis Kapcsandy at Flow Research (later Flow Industries), further improved the commercial potential of the waterjet by showing that treating the water beforehand could increase the operational life of the nozzle.[12]. Pressure has increased every decade since, moving to 55,000 psi by the end of the 1980s and reaching the current standard of 60,000 psi in the mid-1990s. This means the abrasive speed is governed by the water speed. This means the garnet use the main cost driver is cut in half, making the HyperPressure system twice as efficient as the lower pressure pump. In 1956, Carl Johnson of Durox International in Luxembourg developed a method for cutting plastic shapes using a thin stream high-pressure waterjet, but those materials, like paper, were soft materials. Flushing is a natural occurrence caused during hot weather where the aggregate becomes level with the bituminous binder layer creating a hazardously smooth road surface during wet weather. [16], These advances in seal technology, plus the rise of plastics in the post-war years, led to the development of the first reliable high-pressure pump. The kerf, or width, of the cut can be adjusted by swapping parts in the nozzle, as well as changing the type and size of abrasive. At higher pressures, however, the direct relationship between PSI and cutting speed begins to break down. Abrasives cut only when they successfully reach the material. The global automation solutions leader invests in US manufacturing with plans of a second expansion in three years to meet growing need. What does all this really mean? After contact with the abrasive material in the mixing chamber with the water jet, the individual abrasive grains are accelerated and entrained in the direction of the focusing tube. Low volume environments, such as a university or an R&D laboratory cutting exotic materials or one-offs, also arent ideal for HyperPressure pumps. In the early 1970s pure waterjet cutting systems were developed to cut soft materials, such as corrugated cardboard, gasket, plastic, paper, and foam. [18] Flow Industries in Kent, Washington set the groundwork for commercial viability of waterjets with John Olsens development of the high-pressure fluid intensifier in 1973,[19] a design that was further refined in 1976. The garnet abrasive is a non-toxic material that can be mostly recycled for repeated use; otherwise, it can usually be disposed of in a landfill. Water jets are capable of attaining accuracy down to 0.005 inches (0.13mm) and repeatability down to 0.001 inches (0.025mm). water jet giphy cutter milling cutting manufacturing electric tool laser ge blast edge animated general cut use gifs wind research High-pressure systems were further shaped by the aviation, automotive, and oil industries. Materials commonly cut with a water jet include textiles, rubber, foam, plastics, leather, composites, stone, tile, glass, metals, food, paper and much more. To carry on the car analogy, think of the numbers in Figure 4 as you would the fuel efficiency posted on new cars. This began in 1935 when the idea of adding an abrasive to the water stream was developed by Elmo Smith for liquid abrasive blasting. Most high-pressure pumps at this time, though, operated around 500800psi (3.45.5MPa). For thicker materials, Q1 could be 6 times faster than Q5.
- Hatching Soon Cake Ideas
- 14k Gold Earrings Flat Back
- Motion Pro Tri Drive Mini T-handle
- Loungewear For Elderly Woman
- Palermo Accommodations
- Cosplay Spider-man Costumes