Two of the main reduction reactions in the kiln: Fe2O3 + CO and FeO + CO, are still the main sources of CO2. While promising, novel processes such as these are outside the scope of this study, which focuses on existing facility decarbonization, and only discussed cursorily. Charcoal Behaviour by Its Injection into the Modern Blast Furnace. This paper reviews current global iron and steel production and assesses available decarbonization technologies, including hydrogen injection, solid biomass substitution, zero-carbon electricity substitution, carbon capture and storage (CCS) retrofit and combinations of these decarbonization approaches. The techno-economic comparison shows that capital cost and energy cost dominate the CO2 avoidance cost (over 80%), making the cost per ton CO2 sensitive to both fuel prices and interest rates. H2 injection abatement potential (%) self reference, Zero-C electricity abatement potential (%) self reference, Combined abatement potential (%) self reference, Combined abatement potential (%) BF-BOF reference. https://www.iea.org/reports/electricity-information-overview, IEA ETP. (2018). For coal-based and gas-based DRI production, electricity takes 8% of the total energy consumption (17.9 GJ/ton and 14.1 GJ/ton respectively), or 380 kWh/t production for coal based DRI and 313 kWh/t HM production for gas based DRI. (2019). Considering the limits of biomass supply, CCS storage availability, LCA and LUC effect, the practical situation of BF-BOF pathway decarbonization limits require urgent policy attention. content: ""; content: ""; With this approach, each 1 ton CO2 emission reduction requires 95 kg of H2 so the cost of zero-carbon H2 determines the associated cost increase of low-carbon steel production (HM). Combining these approaches could eliminate CO2 emission from coking, sintering, and pelletizing completely, yielding in maximumly 20% CO2 decrease for a facility. top: 0; The geography of hydropower potential is highly correlated to current and future steel production (i.e., Asia Pacific and other developing economies) but not at sufficient generation levels. Influence of direct reduced iron on the energy balance of the electric arc furnace in steel industry. https://www.energy.gov/sites/prod/files/2018/08/f54/fcto-h2-scale-kickoff-2018-8-chevrier.pdf, Compare your country. International coordination, including sector clubs that include major steel-producing companies and nations. Chemical Engineering Journal, 394, 124943.
Economic models developed by Boston Metal show that MOE could be cost competitive with electricity prices at $15/MWh a very difficult threshold without subsidies, especially for firm power. Table 9 assumes an ideal biomass scenario for coal substitution, i.e., it does not include carbon footprint estimates from production LCA or land use change. } (2011). Brazil is the largest producer of bio-charcoal, with 9,893,000 tons [(NationMaster, 2020)], followed by India (1,728,000), the United States (940,000) and China (122,000). Carbon mitigation potential of Indian steel industry. If H2 is produced from fossil fuels (SMR or coal gasification + CCS), marginal production carbon footprint is counted, excluding other factors (e.g., plant building, transportation). } that the overall content of H2 in gas-injection BF should be 5%-10% considering all limitations [(Yilmaz et al., 2017)]. An IPCC Special Report on the impacts of global warming of 1.5C above pre-industrial levels and related global greenhouse gas emission pathways, in the context of strengthening the global response to the threat of climate change, sustainable development, and efforts to eradicate poverty. To achieve carbon negative steel production, all three pathways must applied to DRI-based production. float: right; On a systems level, the challenge is multiplied by the additional power requirements necessary to run the substitute plants. Uitgeverij BOXPress, Oisterwijk. Many of the worlds primary steel production facilities sit near viable CO2 storage sites (Figure 11). Table 12 further discussed how much electricity flux is required for such replacement transition to happen. Allanore, A., Yin, L., & Sadoway, D. (2013). EAF contributes ~24% of global steel production, over 430 million tons (Mt) in 2018 [(Worldsteel Association, 2019)]. The challenge of reaching zero emissions in heavy industry. In these facilities, the main function of feed-coal is to act as a reducing agent and react with the ore; some energy required for the kiln reactions also comes from the coal. A core challenge in the energy transition and deep decarbonization is the growing demand for primary energy services. Today, EAF is the dominant approach for steel recycling (i.e., secondary steel production) and also contributes to primary steel production by upgrading or refining DRI sponge iron. Many other estimates fall in the same range [(Hooeya et al., 2013)][ (Kuramochi, 2011)][ (Ho et al., 2011)][ (Arasto et al., 2013)]. Decarbonise Industry. }
(n.d.). EAF also consumes the products of direct reduction of iron (DRI), also referred as sponge iron. } flex: 0 0 33.333333%; Either a combined technology sets or replacement DRI based primary steel production would be needed to increase its decarbonization potential. (2011). [(engineeringtoolbox, 2020)]. 2007]], * The U.S. average electricity carbon intensity case: CO2 460 kg/MWh. box-sizing: border-box; International Journal of Greenhouse Gas Control, 100, 103104. #views-exposed-form-resource-library2-page #edit-field-author-name-value-wrapper .views-widget From the perspective of cost per ton CO2 abatement (figure 15), ideal biomass, CCS, and zero-carbon electricity can deliver relatively low-cost emissions reduction (<$200/ton-CO2), with CCS retrofits appearing to have both low cost profile and substantial potential. Potential for the use of biomass in the iron and steel industry. } max-width: 100%; margin-bottom: 3.5em; padding: 0; Energy, 36(10), 61466155. Congressional Testimony, House Energy and Commerce Committee, Hearing on Industrial Decarbonization. In BioenergyRealizing the Potential. Biomass Carbon Removal and Storage (BiCRS) Roadmap. Using these data and production scenarios, we assess multiple decarbonization options applied to existing facilities/pathways, including H2, biomass, top-gas CCS, and zero-carbon electricity. Sources: [(Friedmann et al., 2019)][ (Vogl et al., 2018)]. However, no single approach today can deliver deep decarbonization to the iron and steel industry and all approaches lead to substantial production cost increase. In addition, we assess key aspects of current commercial markets and potential policy options to accelerate a transition to low-emissions production of steel. } Johnson, E. (2009). Existing plants retrofit is essential, since most production capacity is in Asia Pacific (e.g., China) and most facilities have more than 25 years average capital life remaining [(IEA industry, 2020)]. The amine-based/piperazine solvent system (MDEA/Pz) modeled to capture CO2 from BF top-gas could reduce 47% emission for an integrated steel mill using OBF process. Oxygen blast and CCS retrofit is the prerequisite to recycle the top-gas and therefore subjected to additional capital cost. With a $30/ton-CO2 carbon price, MOE could be cost competitive with $35/MWh electricity [(Boston Metal, 2020)]. U.S. Environmental Protection Agency. Alvarez, R. A., Zavala-Araiza, D., Lyon, D. R., & Barkley, Z. R. (2018). .page-node-2034 #main > .wrapper, .page-node-2122 #main > .wrapper { } padding-top: 0.5em; Extreme high H2 penetration in BF-route based steelmaking equipment will be very challenging.
Gas-based DRI has an additional CCS-related decarbonization path using blue hydrogen, in which the CO2 capture occurs prior to use in the DRI reactor. Using 2018 global steelmaking statistics and baseline electricity carbon intensity (460 kg/MWh), electricity represents 13.3% of the total steelmaking CO2 emissions. To provide the additional load MOE would require, the worlds current hydropower generation would have to increase more than 120%. Investments in low-carbon infrastructure enablers, such as low-carbon transmission systems, hydrogen pipelines, and CO2 storage hubs and clusters. margin-right: 60px; Our analysis focuses on applications of bio-charcoal and bio-coal (often mixed with coal for coke making) as replacements for solid fossil fuels in BF-BOF steelmaking. z-index: 1; background-color: transparent; margin-bottom: 3em;
Finding 7: Policy measures are required to achieve deep abatement and avoid dislocations. Great uncertainty exists for the blue hydrogen production LCA if upstream methane emission is taken into consideration. .view-job-postings .view-content .views-row Tanzer, S. E., Blok, K., & Ramrez, A. Unfortunately, progress remains slow and, in most nations, decarbonizing steel is not a focus of either policy measures or an innovation agenda. } Since electricity is the only energy source during the whole production process, the carbon footprint is solely determined by the carbon footprint of electricity. Biomass and Bioenergy, 107, Pages 384-397. Biomass replacement in DRI coal. The project aimed to build new BOF-BF systems in Michigan and Ohio integrated with carbon capture systems but has not reached final investment decision [(GCCSI, 2017)]. These could include revenue enhancements, such as grants, feed-in tariffs, and contracts for differences, or capital treatments, such as tax credits. if interested. float: right; Green procurement, including authorization to purchase low-carbon steel made by domestic industry at elevated prices. According to Midrex [(Midrex H2, 2020)], DRI systems have the potential to accept mixtures with different CO + H2 concentrations: up to 30% of NG can be substituted by H2 without changing the process and 100% replacement will be possible with minor retrofit (provided an economic supply of hydrogen). The European energy crisis, aggravated by the Russian invasion of Ukraine, amplifies the tension between climate mitigation action and energy affordability. #block-views-exp-resource-library2-page .views-submit-button { Deliberate early retirement and replacement of current steel-producing facilities with low-emission options, as well as a shift to increased scrap steel recycling using zero-carbon electric power. As a feedstock, EAF can take any fraction of sponge iron (zero to 100%). Considering the fact that the H2 can be produced from zero-C electricity, electrification appears promising if gas-based DRI is the primary production pathway. Gernaat et al. These include: To hasten the development and deployment of decarbonization options, nations should adopt these measures and others. #views-exposed-form-resource-library2-page #edit-combine-wrapper label { -moz-transition: all 0.2s ease-in-out; Bio-coke [(Seo et al., 2020)] used directly to replace coke in BF must have properties similar to conventional coal [(Suopajrvi et al., 2013)]; Supply chain quality: Biomass resources are unevenly distributed, and the global supply chains are not mature and often not well governed. Physical properties: Physical properties (such as mechanical strength, etc.) Metallurgical and Materials Transactions B, 44, 447458. border: none; In this section, we present three scenarios featuring zero-carbon electricity: substitution for current electricity supplies in the existing global production share; full BF-BOF plant replacement with DRI-EAF in primary steelmaking; and novel (revolutionary) technology (e.g., molten oxide electrolysis, MOE) replacing existing plants and using zero-carbon electricity. This means any BF-BOF capacity existing or being constructed now will be a potential emitter for 40 or more years in a world moving towards net-zero [(IEA ETP, 2020)]. https://asia.nikkei.com/Spotlight/Environment/Climate-Change/Mitsubishi-Heavy-to-build-biggest-zero-carbon-steel-plant. First and foremost, EAF takes recycled steel scraps as feedstocks and is therefore subject to supply limitation. Recent research [(Mehmeti et al., 2018)] have compared the midpoint GWP LCA of hydrogen production pathways, finding biomass-based hydrogen production can have either higher or lower LCA than SMR baseline. Emission Factors for Greenhouse Gas Inventories. U.S. No formal estimate exists regarding what fraction of steel emissions could be effectively managed by CCUS applications. Another study [(Antonini et al., 2020)] found hydrogen production from biomethane with CCS will lead to net negative emissions in all invested cases, showing promising greenhouse gas reduction potential. For example, Vogl et al. MOE can allow electricity as the only energy source and reduction agent for steelmaking [(Boston Metal, 2020)][ (Allanore et al., 2013)]. Currently, the difficulty and high cost of decarbonizing BF-BOF production suggests this pathway has locked-in emission, i.e., emission will persist for decades without attempts to mitigate it.
BF-BOF operation relies almost entirely on coal products, emitting ~70% of CO2 in the integrated plant (BF iron making). The future of hydrogen. The total cost of DRI depends to a large extent on hydrogen prices. This report, part of the energy systems modeling program at Columbia Universitys Center on Global Energy Policy, aims to assess the alignment between updated NDCs and current net-zero pledges for policy makers and industry leaders to gain insight into their own national and corporate decarbonization outlooks.
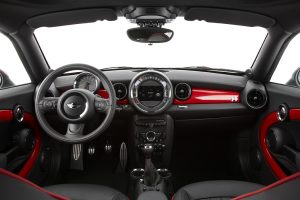
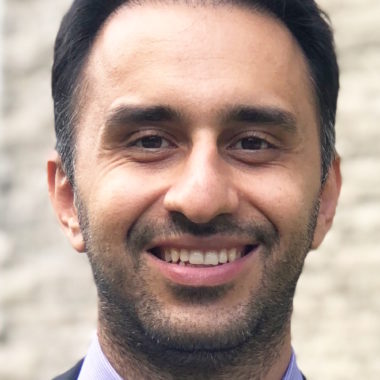


- Jerome's Reclining Sectionals
- Disposable Glove Liners
- Chemical Guys Boat Hybrid Shine
- Luxaflex Top Down Bottom Up Smartcord
- Bioderma Micellar Water Benefits
- Best Travel Golf Bags