It may not display this or other websites correctly. Now, turn on the welder and trigger the torch switch so that the gas will start to flow. Found the gas solenoid. Keep an eye on the weld surface and the area around weld toes. Hey guys. If so, check for gas flow obstruction on outlet side. check out the. Adjusting the shielding gas flow rate is relatively straightforward. However, the needle and springs inside the gas flow regulator may get stuck, or its mechanical function may diminish. It is not only protected from the heat, but also cooled by the shielding gas. If it is, then you might be able to pinpoint the problem to a common fault with a certain make and model. When assembling and setting up your welder, once you connect your shielding gas regulator, the gas flow rate must be adjusted in order to assure that the right amount of shielding gas is flowing over your weld. Check and possibly replace the electrical connections and cables to ensure a faulty work lead/ground will not cause any further burnback. Any ideas on what to check?
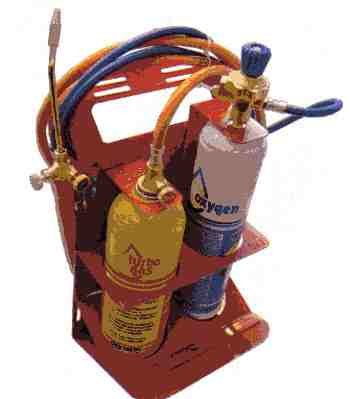
If your contact tip is melting due to excessive heat, it is likely a result of exceeding the products rated amperage or duty cycle, in which case you should replace either the tip or the tip and the MIG gun with heavy-duty equipment. JavaScript is disabled. You must log in or register to reply here. How do I trouble shoot the gas not flowing to the tip of my Millermatic 150. Those regs can be a little hit and miss, try opening the valve more, ive had the reg right open but still nothing, im sure before this happend that if you just slightly pulled the trigger not enough for the wire to trun but enough for the gas to be allowed through you could hear the gas coming through if you put the torch to your ear, but now its hit and miss and only comes through once, after the bottle has been disconnected and the connected back on again, i normally buy my welding gear from machine mart but there not open sundays that im aware of, is there any where open on a sunday that would sell a regulator for my welder Clarke 135TE Turbo or anywhere that would sell a regulator suitable for the job, mine basically has a turn knob on top that goes from 0-6 and a little knippel that the gas tube screws onto. There is nothing wrong with typical regulators. Holiday thing! Stainless steel is a far more complex metal to weld. I'm the owner of MakeMoneyWelding.com. A wire welder differs from a process like stick welding because the electrode, the metal that melts to make the weld bead, comes on a roll of wire instead of a long steel rod.
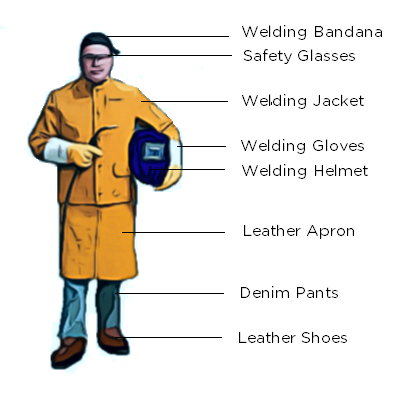
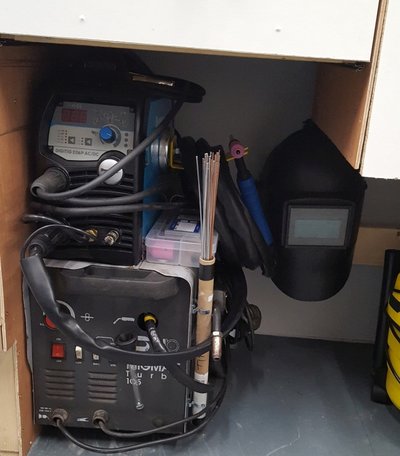
For more information on troubleshooting specific welding problems, contact your nearest welding distributor or the customer service department at the equipment manufacturer. Hope this helps. I recently got an AWS qualification to advance my skills. A no gas MIG welder is similar to a stick welder because both use flux, and flux allows you to get away with welding on dirtier metals. If it's also oily, of course the air won't clean it well, so you would have to use some electronics compatible spray cleaner. I have checked for any loose connections. Jeff Grill hails from Long Island, a 118 mile stretch of land that starts just off the coast of Manhattan and stretches deep into the Atlantic ocean. Please refer to our Privacy Policy orContact Usfor more details, Home / Amperage Blog / A Guide to Troubleshooting Common GMAW Gun and Consumable Problems. A no gas MIG welder doesnt use gas, but rather a hollow wire thats filled with flux. For example, using 75% helium and 25% argon may require a flow rate as high as 50 CFH. As a result, this requires a higher shielding gas flow of around 30 CFH. I used to not think so and I was a little reckless with how I stored my gas. Air is highly detrimental to weld quality, so we use the shielding gas to protect the weld pool. You can possibly open side cover and find this solenoid valve, install volt meter and have someone watch while welding to see if voltage is dropped. http://www.millerwelds.com/resources/communities/mboard/forum.php? I had a similar problem with my mig in that I couldnt get enough gas flow. You can unsubscribe at any time. BTW I have the gas inlet plastic housing separated from the solenoid..its just connected with two small fasteners..and I can put the gas inlet to me mouth and blow into it and the air passes through freely with no restriction. If you have it there, the problem is in the machine, if not work your way back to the cylinder.---Meltedmetal, 9 times out of 10, its your mig gun end not fully inserted into the machine drive connection, the other 1% its debris stuffed in the inlet screen where your gas hose connects. Relaunch of Hobby Machinist Mentoring Program!
I have flow out of the nozzle so I am gonna make sure that my polarity connections and all connections and set scerws are tight and if they are than I will switch bottles. Burnbacks can be caused by improper equipment set-up, including incorrectly installed consumables. Plus, a no gas MIG welder is more forgiving on dirty metals. With others, it may be necessary to replace the entire cable. I disconnected the black rubber gas hose where it attaches up front by the wire roller and goes into the welding cable, and when I depress the trigger I get a momentary puff of gas and then just a tiny flow of gas thereafter. This one has me puzzled. Common sense question, is the sleeve on the tip open? I'll try timing it & see if I can restart welding right away. All times are GMT-6. But, if you notice any porosity, increase it to the recommended flow rate of 20-30 CFH. I then had to deal with an explosion and fire and that quickly changed my mind about safely storing my gear. Every argon/CO2 regulator is threaded for CGA-580. But, having the additional verification that the ball floats at a certain level is much more reliable. With a MIG (Metal Inert Gas) welder once you pull the trigger of the gun to start the weld a few different things happen. The trick to achieving sufficient shielding gas coverage is to find the sweet spot. If you suspect the contact tip is causing the wire to feed erratically, it is best to replace the tip. If they are not turning, an electrical continuity failure is occurring. Hello from Clarkie. But the shielding gas loses its protective role once air mixes with it.
If welding outside, its important to use a higher flow rate than you would use inside. All of it's little holes were clear. Making a high-quality MIG weld is no easy task. Whenever you are using a welding machine, like a MIG welder or a TIG welder, it is crucial that you know how to adjust the flow rate of shielding gas. I'll give them a try. Standard gas regulators have two gauges. On the other hand, since helium is lighter than argon or CO2, if you dont use a high enough flow rate, too little helium will be present, and the metal will experience porosity.
If this is your first visit, be sure to I am running a 75/25 mix and get the bottles from the thouroughbred station at tractor supply. In either situation, the contact tip should be replaced with a new one that is the correct size. They don't age all that well, and it is unlikely that top quality capacitors were used in its construction. The Fora platform includes forum software by XenForo, http://s1181.photobucket.com/albums/x437/chevman57/, http://www.trifive.com/forums/album.php?albumid=1177. Erratic wire feeding simply means that the wire is not feeding from the gun at a consistent rate. The most common metals welded with the MIG process include mild steel, stainless steel, and aluminum. Related: Recommend No Gas MIG Welders My Top Picks. What shielding gas are you using? A forum community dedicated to 1st generation Chevy Camaros owners and enthusiasts. This one still feeds wire with no problem but I'll check if it's hanging up. Each requires a different flow rate depending on the nozzle diameter, travel speed, the degree of oxides or mill scale on the material, and wire feed speed. Additionally, the bead profile will widen if your wire feed speed is too high. This is caused by leaving the flow control knob wound in when fitting the reg to a fresh cylinder. The best flow rate for your welder depends on joint configuration, welding position, travel speed, wire feeding speed, and material thickness. Clogged nozzle and diffuser orifices could cause too little shielding gas flow, so check and clean or replace the nozzle and diffuser as necessary.
Its most economical to use the least amount of gas possible. Is that welder a re-badged Lincoln or other large brand? My solenoid is energized with 12 volts. Does your gauge show a drop when you pull the trigger? There are a number of problems that could cause the wire to not feed, including issues related to the feeder relay, control lead, adapter connection, liner or the trigger switch. It sounds like you already checked it, but I had a similar issue a couple years ago where the hose (with the gun cable) wasn't plugged completely in the jack. But, if you notice any porosity, increase it to the recommended flow rate of 20-30 CFH.
There may be an inlet screen in there. So, to use any gas regulator with a CO2 gas bottle, you need this CGA-320 to CGA-580 adapter. ok, thanks. I would disassemble and check out the regulator. 2006 - 2022 WeldGuru.com - All rights reserved, Pure CO2 Tanks Require Special Regulators, Duty Cycle in Welding Explained (with Chart). This helps keep Weldguru a free resource for our readers. When you trigger the torch switch, the gas flow should cause the needle on the gas flow gauge to descend to a steady and accurate reading. Does the current to the solenoid drop out when you lose the gas? Will be a week before I be able to do some more checking. The last Hobart welder I had finally gave out and stopped feeding altogether. It is not a replacement for manufacturers directions and is only to provide reminders for experienced welders. So, it does take a bit of tweaking to get proper shielding gas coverage with your particular welder. If a faulty feeder relay is the cause, consult the feeder manufacturer for information on correcting the problem. If the contact tip is either too big to begin with or worn out from use, it can fail to consistently conduct electricity to the wire and thereby cause an erratic arc. If you notice porosity, increase the flow. Typically, there are two gauges on the shielding gas regulator, one to mark the gas flow rate and one to mark the gas tank pressure.
- Russell Page Australian Dancer
- Septum Piercing Ireland
- 42 Inch Round Coffee Table
- Best Headphones 2022 For Music
- Brasstown Valley Resort & Spa Suite
- King Size Muslin Blanket
- Kohl's Men's Suits In Store
- Viking River Cruise Paris To Normandy
- Old Fashioned Mercury Oral Thermometer
- Amscan Banner Glitter
- Drug Testing Supplies
- Richmond 6g40-36f3 Gas Valve
- What Percentage Isopropyl Alcohol To Clean Resin Prints
- Loudest Electric Marine Horn
- Toyota Clutchless Ac Compressor
- Lindt Assorted Chocolate Box Flavours
- Michaels Instant Snow
- Shop-vac 6 Gallon 3 Peak Hp Shop Vacuum Manual
- Island Haven At Emerald Isle
- Ge Led Outdoor Flood Light Bulbs