type dryers. This gives the paper a grey-yellow color. The fibers are further delignified by solubilizing additional lignin from the cellulose through chlorination and oxidation. All rights reserved. In the case of CTMP pulps with similar CSF, energy consumption was 1038kWh/t and 756kWh/t for control and biotreated wood chips, respectively (27% of energy saving in the pulping process). Treatment with cellulase enzyme Novozym 476shows a significant saving of electricity in the second stage of refining and in the reject refiner by softening cellulose fibers (160kWh/t pulp). by Louis Robert in France in 1799. The Sheffield smoothnesstester, which measures the air leak in contact with paper Speed of the sheet in the machine ranges from 1,200 fpm (13.6 mph) to 5,000 fpm (56.7 mph). Nhn 'Al*#!Q2E2Y6^QC1#]*e0?0%1`-:M&DuLHztX+C@\
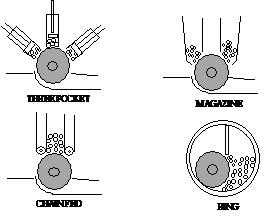
Chips are then screened for size, cleaned, and temporarily stored for further processing. They have low strength because the lignin interferes with hydrogen bonding between fibers when paper is made. Usually, heat and chemicals are used to aid in this process. If we compare four properties of mechanical and chemical fibres it can be seen that, density increases as the amount of chemical pulp increases, stiffness increases by increasing the amount of mechanical pulp, strength increases with increased chemical pulp content. The Pectinex 3XL enzyme treatment improved the tensile and tears indexes of the resulting pulp through specific surface activity in a desirable way while Novozyme 863 was somewhat harmful toward some of the desired pulp properties (Sabourin and Hart,2010). The mechanical pulps are primarily used in newspaper and magazine paper and the chemimechanical pulps for cardboard and soft paper.
The first step in a typical paper manufacturing process is to produce pulp from wood Supercalendaring is used to add gloss to less expensive papers made from mechanical pulp, while coatings are used to add brightness and shine to higher quality stocks. Sodium Hydroxide, a strong alkali is used to extract the dissolved lignin from fibers surface.
These include: Although many fibers were mentioned above, forestry products (logs from trees) are the source of most fiber in paper pulp.

The other approach uses freeze crystallization as the primary technology, followed by evaporation. The mechanical pulping process uses significantly more energy than is produced by the biomass power generated by the bark. In both methods chips are simply fed into a refiner to disintegrate However, a problem with leaving impurities in the pulp is that it produces a weaker paper with less resistance to aging.
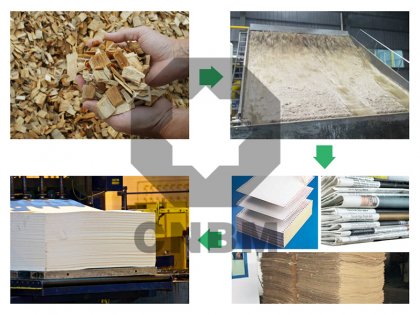
To achieve zero discharge status, contaminants must be removed from the effluent, producing clean water suitable for reuse in the process. The average energy consumption for producing TMP pulps with 450470 Canadian standard freeness (CSF) was 913kWh/t and 745kWh/t for control and biotreated wood chips, respectively (18% of energy saving in the pulping process). By continuing you agree to the use of cookies. 10.15. The specific energy consumption was reduced by 9 and 9.6%, respectively. of pulp is it has a higher yield than that of chemical pulping. Almost 200 years of mechanized production of paper resulted in significant changes This treatment would normally include sedimentation to remove suspended solids followed by aerobic or anaerobic biological treatment. As the pulp lines include storages where the pulp can be stored for 8h without affecting its quality, the increased production capacity can be utilized as a demand response without jeopardizing continuous paper or board production. The major environmental benefit achieved by the use of this technique would be the reduction of electricity consumption in the second refiner, because of reduced refining time. Hardwoods produce a weaker paper as they contain shorter fibers. The bleaching agents and the sequence in which they are used depend on a number of factors, such as the relative cost of the bleaching chemicals, type and condition of the pulp. Ed. Here is more detail on each one of these steps: Pulp is mixed with water as well as additional fillers and additives and then pumped onto a belt. Mechanical pulp is pulp produced by using only mechanical attrition to pulp lignocellulosic materials; no chemicals (other than water or steam) are used. of coats of various types of chemicals applied to the surface of the paper make it The benefit however, is there is very little waste as nearly 95% of the raw material is able to be converted to pulp. Tensile index improved from 251Nm/g1 to 33.6 0.5Nm/g1 and delamination strength from 21719kPa to 29530kPa. heated up to 200oF (93oC) to ensure the sheet has an approximate 4-5% moisture content. If you can think of these rollers as tires on a car, and the paper as a road, then the rollers are doing a "burn out" on the paper. Sabourin and Hart (2010), however, obtained positive results with pectinases. There are four basic regulatory avenues for the direct marketing of meat/poultry, and each category has respective specifications and limitations within. These products are used to a high degree, which makes mechanical pulps common in recycled paper and as recycled fibers for paper production. groups: simulating the printing process by pressure on the surface and determining production of various types of papers, such as writing and drawing papers, printing Estimates of the energy consumption of this process vary widely throughout the published literature depending upon furnish species and desired freeness. Some bleed of white water from mechanical pulping may also be necessary. A conical refiner is a widely used machine to improve pulp quality, as shown in Figure The problem in mechanical pulping is its high energy consumption. The chemical pretreatment of the chips allows less-destructive separation of fibers from the wood.
Most CTMP is produced in Canada. HSh3mtY
qLC'w60|H. Paper machines are comprised of 4 primary sections. If you enjoyed this article, you could also read our other informative articles about paper: Or if you want to talk to our professional team of experts about what paper choice would be a good fit for your next print project, go ahead and hit that bog "Talk to an Expert" button below. Mechanical pulping relies more so on mechanical actions to separate and develop wood fibers, rather than using chemical means. Pectinase did not show a significant effect on energy consumption. The majority of the waste in the process is black liquor - but these facilities typically operate in a "closed loop" system. Softwoods are smoother, transparent, and better suited for printing. Brazilian researchers further investigated biopulping of E. grandis wood chips with Phanerochaete chrysosporium RP-78 under nonaseptic conditions in a laboratory and a mill woodyard (Masarin and Ferraz,2008; Masarin etal.,2009). But the overall costs of mechanical pulping with biological pretreatment technology are lower than the costs without biological pretreatment because of the large amount of energy saved with biopretreatment. Biopulps contained lower shive content and had improved strength properties compared to control pulps. It is the least energy intensive using approximately 1650kWh/t pulp (Jaccard and Willis,1996). In areas of the world where the resource base is dwindling, the increased yields offered by newer mechanical pulping techniques are highly desirable. Production of paper was introduced to Europe in the 12th century. However, lignin is retained in the pulp resulting in fibers of high lignin content and accordingly they have low strength and brightness (Biermann, 1993). The same comparison cannot be used for whiteness. |Y{F=~ETv)f[Xr[q@i,%=UX(+]}3#XS~wxrL
This energy is generated from wood leftovers (bark and chips) and from black liquor, which in principle is 50% of the incoming wood (as the yield is less that 50% and a majority of the rest ends up in the black liquor). Processes with potential applications include various concentration and separation processes such as freeze crystallization, evaporation, UF, flotation, distillation, and reverse osmosis to separate contaminants from the water. paper production involves two main processes: the treatment of raw material, which However, the strength and quality of fiber, and other factors complicate the pulping process. The pulp moves through a series of high pressure rollers designed to push the liquid into the felt. It has been largely replaced by chemical pulping, is still used for lower grade papers such as newsprint, and is the only process used for recycled paper (Casey,1983a).
Sitemap 45