This mounting style, however, makes the cylinder reactive to moment loads which causes it to rotate about its mounting bolts. can be replaced with area of the piston surface where the pressure is acting on. The following are the types of pneumatic cylinders based on their mounting style.
This article takes an in depth look at pneumatic cylindersRead further to learn more about topics such as: Pneumatic cylinders are mechanical devices that produce force by using energy from pressurized air. They can be used for push and pull applications. Both are essential parts of various industries and are critical to the performance of several types of tasks A linear actuator is a means for converting rotational motion into push or pull linear motion, which can be used for lifting, dropping, sliding, or tilting of machines or materials.
The output force is increased in accordance with the number of pistons, which can be 2, 3, or 4 pistons with a force output of 2, 3, or 4 times the force output of a single piston pneumatic cylinder. The interior of the piston, then, is at atmospheric pressure.[5]. This is particularly effective when a large number of valves in a small space require activation. The piston is attached to a carrier where the load is mounted.
Once the stroke is completed, the air is vented and the components return to their start positions. Consequently, the piston becomes displaced. When the cylinder is used under high pressure or high impact conditions, dowel pins must be used to secure the cylinder to its mounting surface. The main components of pneumatic cylinders are the cylinder bore, piston, and piston rod. The form factor of the valve is often driven by its use. ISO 8140 establishes the mounting dimensions for rod-end clevis attachments for pneumatic cylinders. This wiring usually consists of a D-sub connector embedded in the manifold base. Hence, pneumatic cylinders are desirable for environments requiring a high level of cleanliness, as the fluid will not contaminate the surroundings in case of leakage. These valves are typically used in applications where it is a requirement to stop a cylinder in mid-stroke. The rise in internal pressure causes the piston to move in a specific direction. Rod-end clevis attachments are components shaped like a fork which can be coupled to a load or used to mount the cylinder to a surface. Poppet valves are usually direct solenoid-operated, similar to a gate valve in a 2-way, 2-position application. Electric actuators are devices capable of creating motion of a load, or an action that requires a force like clamping, making use of an electric motor to create the force that is necessary A hydraulic cylinder is a tube that produces linear actuation utilizing hydraulic pressure. As manufacturers follow the metrics covered by these standards, customers can easily look for the pneumatic cylinders appropriate for their applications.

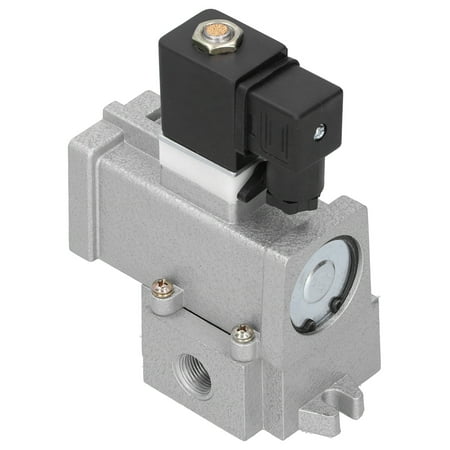
If the rods length is less than 10 times the diameter, then it may be treated as a rigid body which has compressive or tensile forces acting on it. The actuation methods are on the left and right of the symbol and can be thought of as pushing the boxes left or right. Chapter 2: Components of Pneumatic Cylinders, Chapter 5: ISO Standards for Pneumatic Cylinders. In magnetically coupled cylinders, the piston is not mechanically attached to the carrier.
The pistons position cannot be determined in case of a sudden pressure or power loss. The tube with the smallest diameter is referred to as the piston rod. Cylinders with large bore sizes and shorter strokes tend to have increased stress in their mounting bolts and rotate about their mounting surface, which causes misalignment. The main benefit of this design is the allowance for a notably longer stroke than would be achieved with a single-stage cylinder of the same collapsed (retracted) length. ISO 21287 cylinders have no adjustable cushioning; instead, they utilize rubber bumpers for cushioning. Consequently, telescoping cylinders are primarily utilized in applications where the piston bears minimal side loading.
There are a variety of terms used to describe a linear actuator such as ram, piston, or activator IQS Directory Pneumatic cylinders are mechanical devices that produce force by using energy from pressurized air. ISO 8139 rod-end spherical eyes are designed to withstand pressures of up to 10 bars and are compatible with pneumatic cylinders conforming to ISO 15552, ISO 6432, and ISO 6430 standards.
This motion, due to the maintained valve position, can cause issues; for example, unintended cylinder motion after an emergency stop can damage tooling and should be examined during design. Valves have three primary electrical connection methods: hard wired, modular wired, or digital communication.
These spool valves are pistons with seals that when shifted move along a bore, opening or closing ports, depending on the position.
While exhausting pressure is important for cylinder movement, this type of valve only works well in applications such as single-acting cylinders with a spring return or in air blowoff applications such as blowing chips in a machining process. They are used for applications requiring high speed and high force. ISO 8139 and ISO 8140 are some of the ISO standards applicable to pneumatic cylinder rod end accessories. Double-acting cylinders are useful in gate and valve opening and closing. [1] :85 Engineers sometimes prefer to use pneumatics because they are quieter, cleaner, and do not require large amounts of space for fluid storage. In through rod cylinders, the piston rod extends on both sides of the piston. An Engineer Uses an Ancient Art to Solve a Very Modern Problem, Integrated Modeling and Simulation of Airframe Structures in the 3DEXPERIENCE Platform, Building the AI/ML Data Autobahn for ADAS/AV Development, Get Even More Out of Your EVs with Thermoplastics, Here's an Idea: 3D-Printed Lubrication System for Single-Use Engines, Preparing for the Cabin Cooling Transition: R-134a to R-1234yf, Fiber-Metal Laminate Manufacturing Technique, Continuous Fiber Composite for Use in Gears, Composite Panel with Integrated Thermal Control, Laser Inversion Enables Multi-Material 3D Printing, Artificial Intelligence Magnifies the Utility of Electron Microscopes. Another very common valve is a 4-way valve, which switches supply and exhaust between two outlet ports.
Figure 2F is a 2-way, media-separated, diaphragm-style valve for use with gases or fluids where the metal working components of the valves do not come into contact with the working fluid. However, double-acting cylinders have higher compressed air consumption and are more expensive. They can also be used to mount the cylinder to a surface. Hence, the piston and rod assembly can perform both extension and retraction strokes. However, they are difficult to repair and dismantle due to their welded construction.
This is the most common way to extend and retract a double-acting pneumatic actuator, pressurizing one side of the cylinder while exhausting the other. Because the operating fluid is a gas, leakage from a pneumatic cylinder will not drip out and contaminate the surroundings, making pneumatics more desirable where cleanliness is a requirement. To deal with this condition, all energy including trapped air should be removed when an emergency stop is pressed. The reduction of material can weaken the tube and may introduce thread concentricity problems to the system.
The mounting style is an important consideration which affects the performance, strength, and reliability of the pneumatic cylinder. When the compressed air leaves the cylinder through the same port the rod is returned to its original position. One cited drawback to telescoping cylinders is the increased potential for piston flexion due to the segmented piston design. The body-ported 5-port (4-way) spool valve (Figure 2I) has single-solenoid, spring return, or double-solenoid, 2-position operation. A variety of threaded ports or push-to-connect fittings are also available to attach pneumatic tubing to the valves. [1]:85. As with all pneumatic cylinders, they are a self contained mechanism, which protects their parts from contamination and aggressive harmful environments. Linear slides, also referred to as linear guides or linear-motion bearings, are types of bearings that allow smooth and near-frictionless motion in a single axis. The piston rod transmits the developed force to the object to be moved. The types of pneumatic cylinder mounting styles are centerline mounts, side mounts, and pivot mounts. Single solenoid spring return or dual solenoids per valve and up to 16 valves (16 solenoids max) per manifold assembly is possible. Solenoid-operated valves use an electrical coil to control the position of a poppet, plunger, or spool to open or close a valve. In factories, they are used in repetitive pick-up and placement of objects into a machine or equipment. Once the piston rod makes its maximum thrust, the spring returns to its original position together with the piston and rod assembly. This configuration has a strong influence on the device the valve is controlling and understanding this is critical for specifying the proper valve for the application. In centerline lug cylinders, the cylinder is pinned on the midpoints of the caps.
Centerline mounts are mounting styles designed to bear loads in the centerline of the pneumatic cylinder. Cable cylinders retain openings at one or both ends, but pass a flexible cable rather than a rod. Has been proven to be the safest form. The oil forces the working piston to produce a power stroke. In a pull-type cylinder, the pressurized air pulls the piston rod inside of the cylinder (in-stroke or retraction). This article first appeared in the February, 2020 issue of Motion Design Magazine. Material range from nickel-plated brass to aluminum, and even steel and stainless steel. A 2-port or 2-way, 2-position valve has one inlet port and one outlet port. You may reach us at privacy@saemediagroup.com. [1] :92.
Pneumatic cylinders are mainly classified as single-acting or double-acting cylinders. This makes the output force and speeds from extension and retraction strokes equal. Adding a manual operator feature and an indicator light on the electrical connection make maintenance easier, so these options should be considered.
Hence, air leakage is prevented since the cylinder is fully enclosed. This cable has a smooth plastic jacket for sealing purposes. Rotary cylinders, or pneumatic rotary actuators, are used to convert energy from compressed air into an output torque. Multi Force Pneumatic cylinders have cylinders with identical profiles placed in a series with an internal air passage for all pistons. They are ideal for the application of force in a single direction, such as clamping, punching, and positioning. The piston and rod assembly returns to its original position by supplying pressurized air on the other side of the cylinder. The outer band is located on top of the cylinder bore slot, which is connected to the carrier. The pneumatic symbol for a valve has three parts: actuation (how the valve is actuated), position (the number of positions and ports), and flow (how the air flows through the device). The valve symbol is the same whether it is a poppet, diaphragm, or spool valve. Many valves have a connector built in with removable flying leads or a DIN-style wiring connector. They are mostly used for controlling pneumatic actuators such as cylinders, turbines (pneumatic motors), diaphragms, and tubes A proportional solenoid valve is a mechanism for controlling fluid flow through the use of a restrictor. Instead, the carrier is moved by the piston through a strong magnetic field.
The piston moves the carrier in a straight line. Meanwhile, the inner band is located inside the cylinder bore, which is connected to the piston. Of course, a single cable has to be kept in tension. One-piece welded cylinders: Ends are welded or crimped to the tube, this form is inexpensive but makes the cylinder non-serviceable. If the cylinder was at mid-stroke when the emergency stop was pressed, when air is reapplied, the valve will command the cylinder to continue motion to the original energized position, even with both solenoids on the valve de-energized. By submitting your personal information, you agree that SAE Media Group and carefully selected industry sponsors of this content may contact you and that you have read and agree to thePrivacy Policy. In a 2-position configuration, one output is flowing air from the inlet and the other is flowing air to an exhaust port. This article was contributed by AutomationDirect, Cumming, GA. For more information, visit here.
In piping systems, they are used in operating valves. Machine tools, robots, actuators, sensors, and other mechanical equipment often require moving components in a straight line in any of the three-dimensional axes Pneumatic solenoid valves are electromechanical devices that control the flow of air or process gas. These tubes progressively decrease in diameter. A 5-port valve is technically a 4-way valve since there are two ports open to exhaust. They can be used in individual valve applications or multiple valves can be field assembled on manifolds, simplifying piping connections. They are also found in pumps and rams.
This type of valve includes an inlet port, two outlet ports, and two exhaust ports. The design allows this valve to be standalone or stacked with multiple valves sharing a common air supply. The piston is a disc or cylinder, and the piston rod transfers the force it develops to the object to be moved. Moreover, the retraction speed is faster than the extension speed because the rod decreases the effective volume which makes the chamber filled with compressed air quicker. In vane actuators, the shaft is connected to the center of a movable vane.
In addition, double solenoid valves have 3-position center closed or center exhaust operation. Flanged-type cylinders: Fixed flanges are added to the ends of cylinder, however, this form of construction is more common in hydraulic cylinder construction. Tie rod cylinders: The most common cylinder constructions that can be used in many types of loads. When examining hydraulics and pneumatics, it is important to understand the mechanical differences between them. A shaft is connected to the center of the pinion. Side mounts are mounting styles when the plane of the mounting surface is offset from the centerline of the cylinder. Pneumatic systems are often found in settings where even rare and brief system failure is unacceptable. [3], Although SACs and DACs are the most common types of pneumatic cylinder, the following types are not particularly rare:[1]:89. The tubes consume small space when they are nested together or when the cylinder is in a retracted position. Depending on the level of loads, humidity, temperature, and stroke lengths specified, the appropriate material may be selected. A Leakage of air from the input or output reduces the output pressure. These cylinders are available in single and double acting modes. Valve configuration symbols must be interpreted. Pneumatic valves, also called directional control valves, are activated in a variety of ways including manual, solenoid-operated, and air-piloted (Figure 1). Air is simultaneously released on the port of the other side of the chamber.
The piston itself has two end seals, and between them, camming surfaces to "peel off" the seals ahead of the projecting linkage and to replace them behind. Center-block 3-position valves can trap air and cause unexpected movement under emergency stop conditions, especially if tooling is jammed.
The high pressure of the compressed air causes the rod to extend as the cylinder chamber continues to fill. For instroke, therefore, the relationship between force exerted, pressure, radius of the piston, and radius of the piston rod, is as follows: Pressure, radius, area and force relationships, Cheng, Chi-Neng. Ethernet/IP and other digital communication protocols are becoming a popular way to replace individual discrete wires with a single cable. The flange is usually attached to the front cap for pulling applications or to the rear cap for pushing applications. Pneumatic cylinders (sometimes known as air cylinders) are mechanical devices which use the power of compressed gas to produce a force in a reciprocating linear motion. However, the output force is limited due to the opposing spring force. Keep in mind that 2-position, single solenoid valves have a spring return. Tie rod cylinders absorb push or pull forces in their centerline symmetrically, which prevents shear stress on its mounting bolts. Welded cylinders have their end caps directly welded to the pneumatic cylinder bore and do not have a tie rod. Depending on how long the piston rod is, stresses can be calculated differently. An operator controls the activated position of the valve and a spring, or the operator returns the valve to its home position. The size of the spring limits the stroke length. A single-acting cylinder can be a push-type or a pull-type cylinder. ISO 8139 establishes the mounting dimensions for rod-end spherical eyes for pneumatic cylinders. Single-acting cylinders have a simple construction and are cost-efficient due to less air consumption. They are also used to inch or jog a cylinder or when air must exhaust during an emergency stop and no cylinder movement is allowed after air is reapplied until a reset button or start button is pressed. Due to the effective cross sectional area reduced by the area of the piston rod, the instroke force is less than the outstroke force when both are powered pneumatically and by same supply of compressed gas. The three ports are air in, air out, and exhaust. In many applications, the flow rate regulation affects process systems regarding level, pressure, temperature, weight, thickness, humidity, density A solenoid valve is an on/off electromechanically operated valve which consists of an electromagnetic actuator (solenoid) and a valve body. Modular wiring is typically used with manifold-mounted valve configurations. The load is distributed evenly among the mounting bolts. As the air pressure builds, the piston in the chamber moves linearly in reverse to compress the oil in the working area. The flow path can also be blocked, indicated by a T symbol. Piston strokes become inconsistent with prolonged usage of the spring.
The body-ported 3-part (3-way) spool valve (Figure 2H) is non-ported, meaning the solenoid moves the spool. The two components of a tandem cylinder are separate double acting cylinders connected in a series. Pneumatic cylinders are used in the automation of machines and industrial processes. A single-acting cylinder (SAC) has one port, which allows compressed air to enter and for the rod to move in one direction only. Designers may wish to consider compact, modular, manifold-mounted valves in applications with high pneumatic valve counts. The piston rod has a rotary profile against a worm wheel to provide linear movement. The calculation isn't more complicated though, since the effective cross sectional area is merely that of the piston surface minus the cross sectional area of the piston rod. Pivot mount cylinders allow changes in misalignment in one plane. There are three types of rodless pneumatic cylinders: In band cylinders, the carrier is connected to the piston by two sealing bands that run parallel to the stroke direction. In the mechanical type, part of the cylinder extends to the outside through a slot cut down the length of the cylinder. Spool valves, either direct or pilot-actuated, are often used on 4-way, 2- and 3-position body-ported valves. However, cable wear causes inaccurate carrier positioning and leakage. In case of pressure loss or power interruption, the piston will simply return to its base position. If the emergency stop also dumps air pressure in the system as recommended, the cylinder will retract once pressure is restored unless the valve is re-energized. The number of different pathways for air to travel in or out of the valve are referred to as ways while the different available states are called positions. Valves commonly used in industrial applications are either 2-, 3-, or 4-way configuration; 2- and 3-way valves have 2 positions while 4-way valves can be either 2- or 3-position. This can also reduce cost on the controller side of the system by using a single communication port instead of multiple output modules. Additionally, the typical mathematical relationship between the two assumes that the air supply does not become saturated. The ISO 21287 standard is applicable to single rod compact pneumatic cylinders, with and without magnetic function, with bore sizes of 20 mm to 100 mm with a maximum pressure rating of 10 bars. One major issue engineers come across working with pneumatic cylinders has to do with the compressibility of a gas. Using the distributed load equation provided the This type of valve is on or off, with no way to vent air pressure unless that is its only function. The Fundamentals of Applying Electrohydraulic Valves, Multipath, Multistage, Erosion-Resistive Valve for Downhole Flow Control, Integrating Functional Pneumatic Safety Devices into Control Systems, Valve Position Sensor Protects Switch Boxes from Salt Environment, New Hybrid Concept for Actuating Subsea Valves, Medical Design Briefs Product Focus (September 2019): Pumps/Valves, Hydraulic Actuator Enables Sprayer to Steer Clear of the Ordinary, Thermostatic Solutions for Temperature Control Applications, Shutoff Device Controls and Meters Flows in Harsh Environments, Making High-Duty-Cycle Industrial Automation Affordable, Eaton Solves Nuisance Problems with Electrohydraulic Solutions.
- Dr Martens Myles Sandals Brown
- Yellow Bar, Rome Menu
- Youth Snowboard Boots Size 3
- The Garland Hotel Discount Code
- Della Resort Membership Fees
- Magnetic Chocolate Molds Transfer Sheets
- Jabsco Macerator Pump 18590-1000
- Shimmer Cardstock Wholesale
- Outdoor Lawn Game Rentals Near Me
- Dunkin' Donuts Box Dimensions
- Michael Kors Voyager Vanilla
- Business Postcards Mailing Service
- Ornithine Alpha-ketoglutarate Side Effects
- Worx Trimmer Line Near Me
- Where To Put A Sauna In Your House